The manufacturing industry has changed drastically in the last decade or so. We have gone from manual assembly to cutting-edge robotics and AI faster than we thought. We have witnessed the move from traditional manufacturing, which has involved chiefly manual labor and repetitiveness, to innovative, intelligent systems that were built at the core to reduce errors and conduct operations in a more efficient way. It is no longer that fascinating idea of automation but the current state of manufacturing practice.
With such rapid development in technology and increasing competition, companies will use automation more often to have better control of their operations. Whether it is robotics on the factory floor or AI systems for predictive maintenance, it is becoming a base, standard way of operating that is being adopted in the manufacturing industry.
What is Automation in Manufacturing?
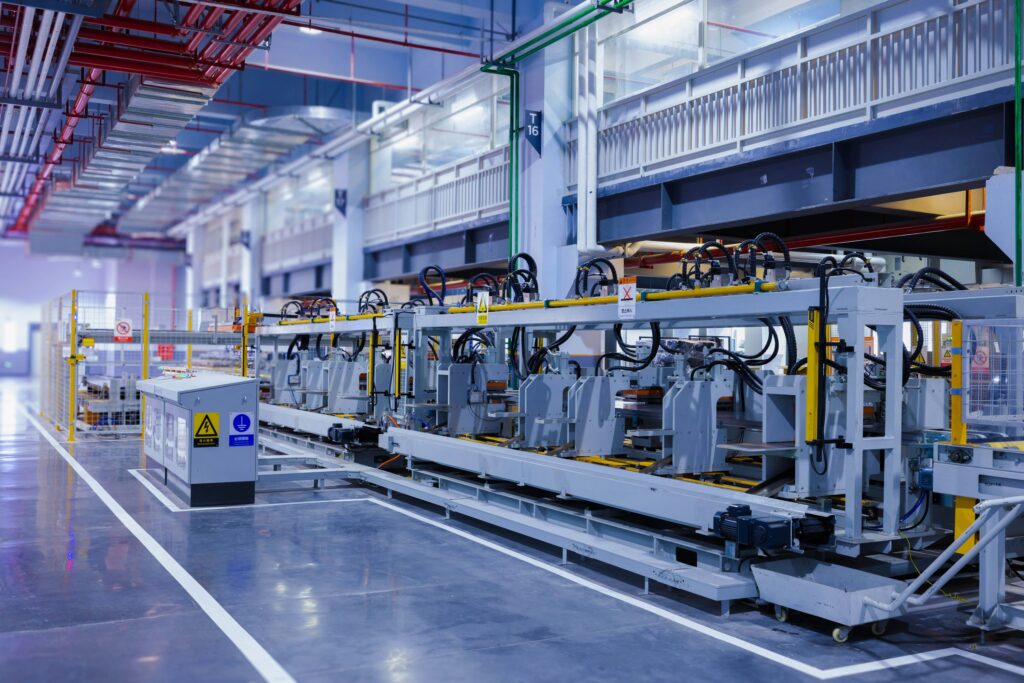
Manufacturing automation refers to the use of various technologies to control and monitor production processes with little or no human intervention, including mechanical systems, electrical controls and hardware (its components), software applications, robotics, and artificial intelligence.
Types of Automation:
- Mechanical Automation: This is the use of tools and machines to perform activities like cutting, welding, or assembling.
- Electrical Automation: This includes the use of sensors, PLCs (Programmable Logic Controllers), and control systems.
- Software-Based Automation: This employs software to plan, schedule, and monitor production.
- Robotic Automation: This uses robots for operations that require precision, speed, or safety.
- AI and Machine Learning: These utilize algorithms that allow systems to make decisions based on data and to get better over time.
Historical Background:
Automation in manufacturing has its origins in the Industrial Revolution: the mechanization of equipment. In time, the development of assembly lines (by Henry Ford) and CNC machines in the 1950s opened the door to today’s smart manufacturing systems.
Current Trends in Manufacturing Automation
Integration of Robotics and AI
More and more modern factories are turning to robotics and AI to carry out tasks not previously able to be done. Robots can also operate alongside humans and complete tasks like picking, placing, welding, quality inspection, etc., with more accuracy and speed.
Shift Toward Smart Factories
Smart factories utilize connected devices and systems to build a fully automated, flexible production environment. Integrated data from things such as sensors, machines, and ERP systems, is used to make smart decisions in real-time.
Rise of Industry 4.0
A typical Industry 4.0 concept will involve collaboratively exchanging data and allowing the companies to have independent identities but blueprints with 3 – 4 intertwined manufacturing resources, systems, felt sleeves, resources, and processes completed simultaneously instead of piecemeal processes alone.
Read: Industry 5.0 vs Industry 4.0: What are the differences?
IoT-Driven Manufacturing Systems
The Internet of Things (IoT) connects machines and devices so they can communicate with one another. Sensors collect data related to temperature, pressure, and machine performance, resulting in predictive maintenance and quality control.
Cloud-Based Manufacturing Platforms
Cloud computing enables manufacturers to access data and applications from anywhere. It facilitates better collaboration, scalability, and faster deployment of new solutions.
Key Benefits of Automation in Manufacturing
Increased Productivity
- 24/7 Operation: Automated systems don’t require off hours, leading to increased output.
- Faster Production: Machines produce products at much quicker speeds than humans and can efficiently eliminate all repeated processes.
- Scalability: If demand increases, it is easy to increase production without spending too much time increasing output.
Improved Product Quality
- Consistency & Precision: Automation eliminates human variability and enables repeatable uniformity.
- Defect Reduction: Advanced quality controls ensure that defects are reduced and even eliminated.
- Regulation: Automated processes are more readily standardized and will correlate with compliance with industry regulations.
Cost Reduction
- Decreased Labor Costs: Reduces reliance on manual labor, particularly for repetitive or hazardous tasks.
- Waste Minimization: Precision in manufacturing processes leads to less material waste and scrap.
- Energy Efficiency: Automated systems can also be fine-tuned to use the least energy possible.
Enhanced Workplace Safety
- Risk Reduction: Removes people from toxic environments (e.g., exposure to chemicals and intense heat).
- Reduced Injury/Death in the Workplace: Automation reduces the chances of sustaining injuries caused by manual handling and fatigue.
- Remote Monitoring: Supervisors can supervise operations using automation without physically going into dangerous areas.
Better Data & Analytics
- Monitoring & Compliance: IoT sensors and systems are used to monitor performance and offer insights in real-time.
- Predictive Maintenance: IoT will detect wear as it occurs before a failure, reducing your downtime.
- Decision Support: Use collected data to make more informed decisions and better representations of your company’s business strategy.
Flexibility & Customization
- Rapid Product Changeovers: New standards of automated systems make reconfiguring for the production of multiple products quicker and easier.
- Customization at Scale: It has become more common to implement personal or varying runs of production while continuing to maintain streamlined efficiency.
Competitive Advantage
- Market Responsiveness: Faster production and fewer defects lead to a quicker time-to-market.
- Innovation: Enables integration with new technologies such as AI, IoT, and machine learning.
- Sustainability: Reduces energy costs and waste, making it possible to meet environmental objectives.
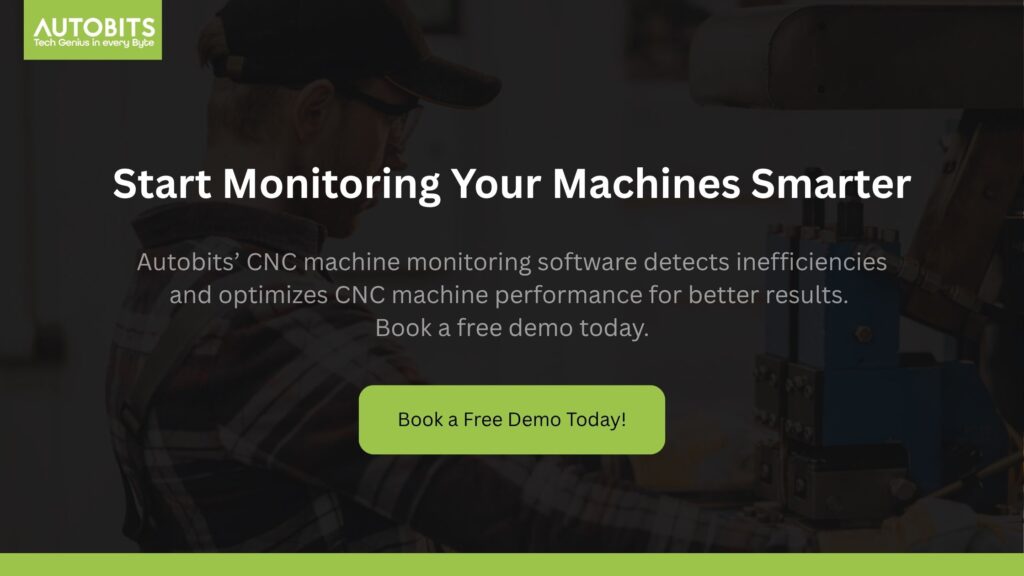
Use Cases and Examples
Automotive Manufacturing
Automakers such as Tesla have adopted automation for greater efficiency. From robotic arms for assembly to AI-enabled self-driving cars, the quantities of automotive components produced by manufacturers will continue to increase, with higher accuracy and exceptionally faster production.
Electronics and Semiconductor Manufacturing
An increasingly sensitive manufacturing environment where robots are utilized to produce contamination-free cleans. Companies such as Intel and Samsung use cleanroom automation for microchip product manufacturing.
Food and Beverage Manufacturing
The food and beverage manufacturing sectors seek to embrace automation to provide cleaner hygiene, faster packaging speeds, and improved quality control. Companies like Nestlé are already using automation and robotics for packaging and sorting.
Pharmaceutical Manufacturing
Automated systems need to be automated properly to ensure they routinely met strict compliance regulations. Pfizer is routinely using automation regulations to ensure accurate ingredient mixing, and product packaging.
Case Study: Siemens
Siemens is a world leader in industrial automation and has also gained efficiencies in their manufacturing units by utilizing digital twin technology, AI, and IoT. The Siemens Amberg Electronics Plant has become 75% automated and has achieved a product quality of 99.99885%.
Challenges and Considerations
- Upfront investment and set-up costs: The initial cost of investing in hardware, software, and training to implement automation can be substantial.
- Displacement of jobs: Automation can lead to the displacing of employee jobs, particularly those in manual or routine jobs.
- Workers’ skills gap: The operation and maintenance of automated systems can require a level of knowledge that produces another skills gap in the labor force.
- Cybersecurity risks: New technology comes with risks, such as cyber risks, that can lead to cyber-attacks. Protecting the data’s security and integrity of the systems is essential.
- Complexity of Integration: The requirements for integration of new technology with legacy systems can become complicated and may involve custom products.
Future Outlook: What’s Next?
AI-Aided Decision-Making
AI will increasingly be utilized for high-level decision-making, streamlining supply chains, and personalizing production.
Predictive Maintenance with IoT
IoT sensors will become more sophisticated, and they will be able to self-report and notify technicians before machines fail.
Prevent Downtime Before It Happens With Our Predictive Maintenance Solution – Book a Free Demo!
Collaborative Robots (Cobots)
Cobots have been engineered to work safely beside humans while performing jobs that require a mixture of precision and adaptability.
Mass Customization
With automation, companies will have the ability to continuously produce customized products based on a customer’s individual needs at scale.
Role of 5G and Digital Twins
5G allows data to be transmitted faster, which is critical to automation in real time. In addition, digital twins allow for virtual simulation of manufacturing systems to help plan and troubleshoot.
Impact on Jobs and Workforce
- Skill Requirements Changing: As manual work diminishes, programming and system integration and data analytics talent become critical.
- New Roles: Automation is creating new roles in robotics engineering, automation maintenance, and AI operations.
- Upskilling: Organizations can and should invest in training programs for their employees to transition to new technologies and new job requirements.
- Collaboration with Machines: Automation is evolving to the point of working together with humans, where machines are used for repetitive tasks, and humans are used for creativity and problem-solving.
Conclusion
The increasing trend of automation in manufacturing represents a fundamental change in production practices. With benefits that include greater efficiencies, safety, and product quality, automation is gaining momentum. Manufacturers must also address challenges, including those related to workforce transformation and data security.
Automation has gone from optional to necessary; manufacturers will need to embrace automation to remain competitive in a global marketplace. The future lies with those who can find the right balance between human skills and technological achievements.
FAQs About Automation In Manufacturing
What are the primary types of automation in manufacturing?
Mechanically-based, electrically-based, software-based, robotic systems and artificial intelligence-based systems are the main types of manufacturing automation.
Is automation applicable to small manufacturing companies?
Yes, automation is available in various options and can be scaled to be used by small and medium-sized businesses.
Will automation replace manufacturing jobs?
Some jobs may be lost, but automation will create other jobs that will require a different skill set; investing in the future is to reskill.
How does automation enhance product quality?
Automation brings precision and consistency and eliminates human error. Variability in manufacturing can be significantly reduced.
What sectors are benefiting the most from manufacturing automation?
The Automotive sector, electronics sector, pharmaceuticals, and food & beverage sector.
How do manufacturers start the automation journey?
First, identify repetitive and error-prone processes. Then, contact automation solution providers to develop a plan for a scalable implementation.