Machine monitors are transforming the manufacturing sector in India by offering real-time data on machine performance, reducing downtimes, and increasing productive outcomes. Regardless of whether you are a small manufacturer or a large manufacturing unit, applying a machine monitoring system to machines like CNC could streamline your work tasks. This guide offers a step-by-step process for successfully implementing machine monitoring software.
Steps to Implement a CNC Machine Monitoring System
Before we get into the detailed steps, here is a quick video guide that visually explains how to set up a CNC machine monitoring system. Watching this video will give you a clear overview of the entire process.
Step-by-Step Installation of CNC Machine Monitoring System [Video]
Define Objectives
Before you use machine monitoring software, be clear about your main goals. Do you want to reduce downtime, improve predictive maintenance, or increase productivity? The clearer you are about your goals, the more you can shape the system to fit those goals.
- Decide how you will measure key performance indicators (KPIs) such as utilization, spindle speed, temperature variations, or vibration.
- Make sure the monitoring system also addresses any compliance consideration that may be industry specific.
Critical and Important Data Points to Collect
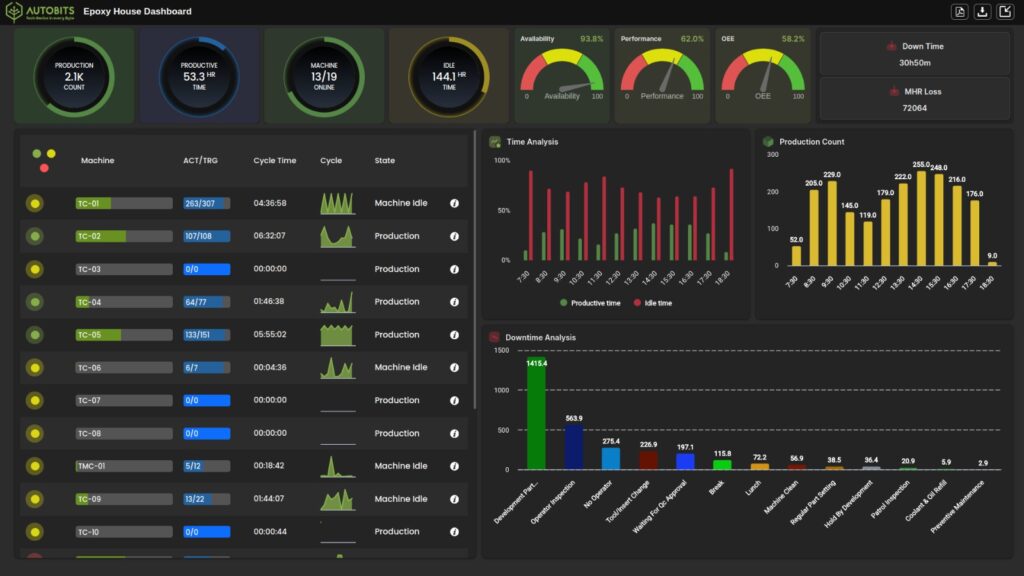
Once you have precise goals, you must identify the specific types of machine data that you want (or need) to track to achieve those objectives. Below are some of the key and vital data points to track:
- Machine uptime and downtime
- Spindle run-time
- Cycle times
- Temperature readings
- Vibration levels
- Tool usage and wear data
- Power consumption
- Alarm and error logs
Important KPIs to Monitor
To track progress against your objectives, it’s essential to monitor relevant KPIs. Some important KPIs include:
- Machine utilization rate
- Overall Equipment Effectiveness (OEE)
- Mean Time Between Failures (MTBF)
- Mean Time to Repair (MTTR)
- First-pass yield (quality of output without rework)
- Setup time reduction
- Energy efficiency metrics
Analyze CNC Machine Capabilities
Knowing what your CNC machine can do is essential to smoothly set it up with the monitoring software.
- First, identify the CNC machine’s control system and verify the data transfer protocols supported, e.g., OPC UA, MQTT or TCP/IP.
- Second, determine whether you can integrate your CNC machine with the existing enterprise resource planning (ERP) or manufacturing execution systems (MES).
- Third, assess and consider whether additional sensors are needed or if you can incorporate any built-in capabilities of the machines.
Select Monitoring System Components
Selecting the appropriate hardware and software tools is imperative for effective supervision.
- Hardware: Determine the sensors you wish to include (e.g., temperature, vibration, tool wear) and where these data nodes will be deployed.
- Software: Choose metrics boards that are based on web technologies or IoT-based platforms that support both real-time analysis and historical data storing.
- Cloud vs. On-Premise: Select a cloud service for remote monitoring, or an on-premise system for maintaining more local control of your data.
Network and Communication Setup
It is important to establish a strong communication chain for the correct transmission of data.
- Use communication protocols such as Ethernet TCP/IP, FOCAS by Fanuc, OPC UA, Open Protocol, etc.
- Use a wireless connection if it is not practical to run a cable (433MHz ISM band, Wi-Fi, or LoRaWAN).
- Use edge computing devices collecting data locally (on site) prior to storing those data in the cloud.
Install Hardware
When monitoring hardware is well installed, it leads to highest accuracy of data.
- Install sensors at key reference points on spindles, tool heads, and machine axes.
- Provide a stable power outlet for the wireless sensor nodes and IoT gateways on site.
- Make certain sensors are calibrated and in proper working condition, and not in need of calibration to record the sensor readings accurately.
- Use hardware that can store data to avoid losing any information.
- Pick devices that can process data on their own (edge computing).
- Choose systems that let you add more sensors later if needed.
Configure Software
Properly configuring the software contributes to efficient machine data collection and visualization.
- Designate polling intervals for collecting sensor data (e.g. every second, minute, or hour).
- Create a centralized dashboard for convenient data visualization and reporting
- Implement real time alerts for exceptions (i.e. high temperature) and anomalies (i.e. excess vibration).
- Create reports based on data acquired.
Test and Optimize
Perform comprehensive performance validation tests before full-scale use.
- Pilot test on a select number of machines and review the data output.
- Tweak the updates on sensor polling and the transmission of the data to eliminate latency issues.
- Tweak and improve the visualizations to present only the most applicable metrics to the operators.
Train Operators
- Training operators guarantees a smooth transition and full use of the software.
- Hands-on training will include how to use dashboards, interpret graphs, and create reports.
- Operators will learn how to resolve minor issues and escalate major system errors.
- We encourage the use of the system regularly to get the most value out of the investment.
Monitor and Maintain
Ongoing monitoring and upkeep are the best methods to avoid unexpected failures of a system.
- Keep sensors clean and check for dust, loose wires, and malfunctions.
- Update the software on a regular basis to enable new features and installation of security patches.
- Expand the system when necessary with additional machines and improved capabilities of sensors.
Key Considerations for Implementing Machine Monitoring Software
1. Data Protection
Protecting machine data is essential, particularly when leveraging cloud-based solutions.
- Utilizing encrypted communication protocols, such as HTTPS and SSL.
- Implementing role-based access controls will help to prevent unauthorized changes to the system.
2. Scalability
Ensuring the system is scalable as the business grows is an important consideration.
- Choosing modular software that allows for easy addition of new sensors or machines without the need for extensive reconfiguration.
- Being flexible, as solutions that can handle multi-factory monitoring could be helpful if the business decides to expand into more than one location.
3. Expense Management
Balancing cost with long-term achievement of ROI is important.
- Switching to CNC system-integrated monitoring instead of costly external sensors, where possible.
- Considering subscription-based cloud solutions if the cost of investment is important currently.
FAQs
What is Machine Monitoring Software?
Machine monitoring software is a software-based tool that gathers and examines machine data in real-time to improve performance, decrease downtime, and increase operational efficiency.
How does machine monitoring help with predictive maintenance?
As monitoring software continually measures machine parameters, including vibration, temperature, and tool wear, it can predict failures and plan maintenance events before the machine experiences a breakdown.
Will CNC machine monitoring software work with all machines?
Nearly all new CNC machine tools can be monitored, but it all depends on the control system and the protocols for retrieving and analyzing data. Old machines may need additional hardware and software for machine monitoring to be used.
Can small manufacturers afford machine monitoring systems?
Yes, cloud-based options and software integrated with CNC systems mean small manufacturers can implement machine monitoring systems without the high cost of traditional monitoring systems for machines.
What industries benefit most from machine monitoring software?
The industries that benefit most from CNC machine monitoring software are the automotive, aerospace, electronics, and precision engineering industries, where accuracy is critical to production.
Overall, by following these steps and best practices, Indian manufacturers can functionally implement machine monitoring software to improve productivity, reduce operational costs, and increase the life of their machines.