- Predictive Maintenance
Predictive Maintenance Solution
Stay Ahead with Advanced Predictive Maintenance Technology
Enhance Efficiency With Our Predictive Maintenance Solutions
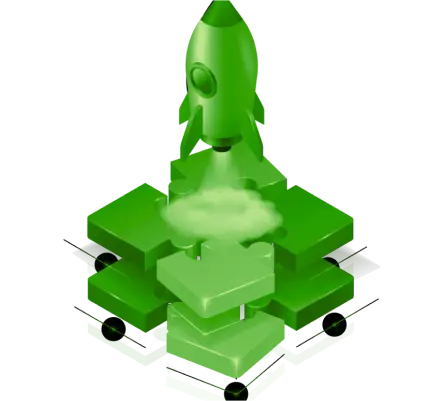
What Is Predictive Maintenance?

Benefits of Predictive Maintenance

Increased Efficiency

Reduced Downtime

Cost Savings

Improved Safety

Increased Machinery Lifespan
Autobits' Predictive Maintenance Works
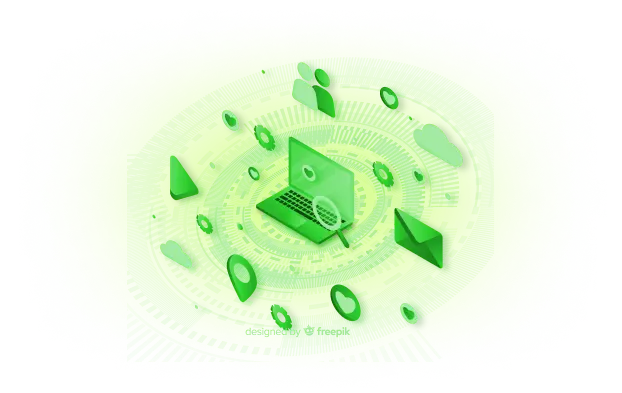
Continuous Data Collection
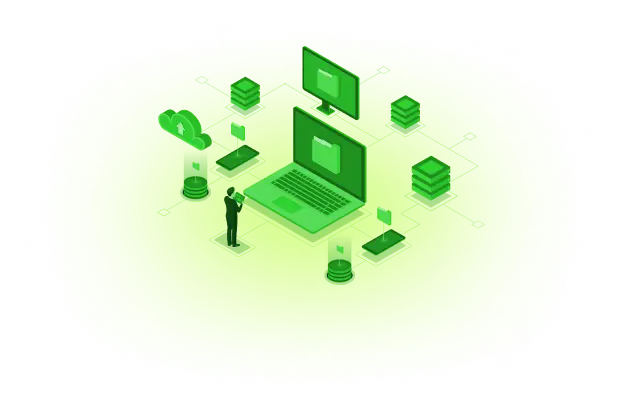
Predictive Alerts
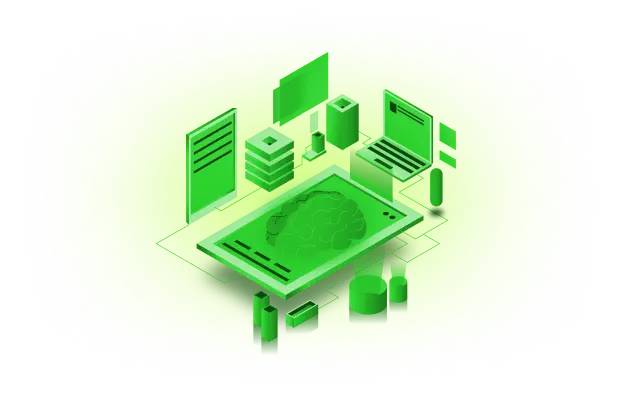
Real-Time Data Analysis
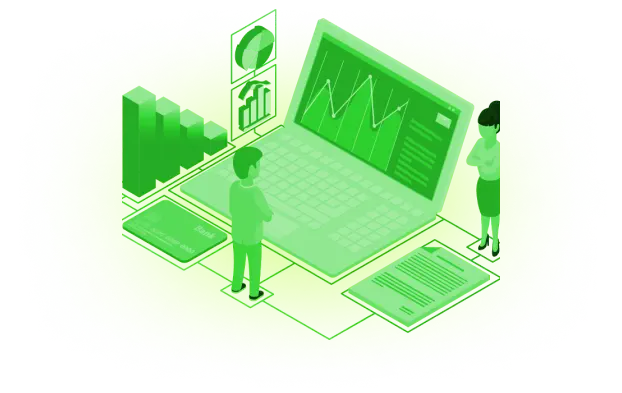
Integration with Existing Systems
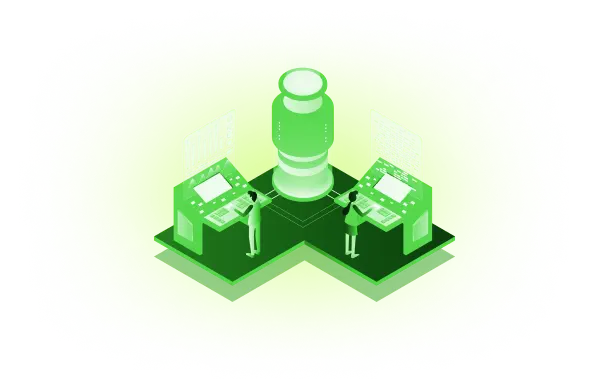
Customized Maintenance Proposals
Alert and Notification feature of Predictive Maintenance
Our cutting-edge software integrates several tools and features to streamline maintenance tasks and increase operational effectiveness.
Reports of Maintenance Activity
Maintenance Scheduling
Mobile App Integration
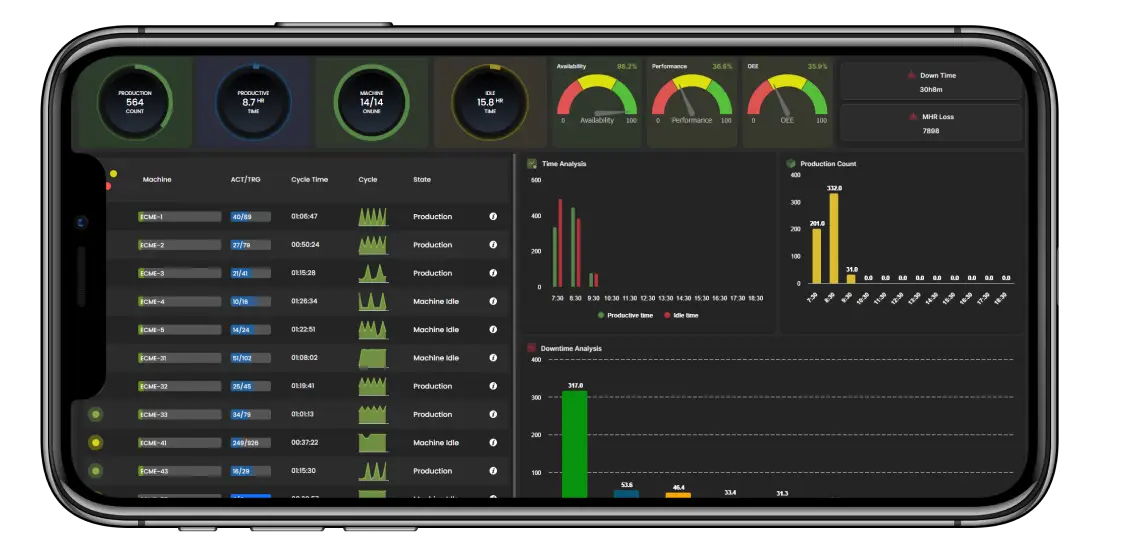
Maintenance Reminders
Triggers on Maintenance Activity
Integrate Maintenance with IoT
Join the 400+ companies that are already expanding






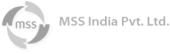
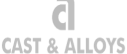
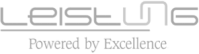

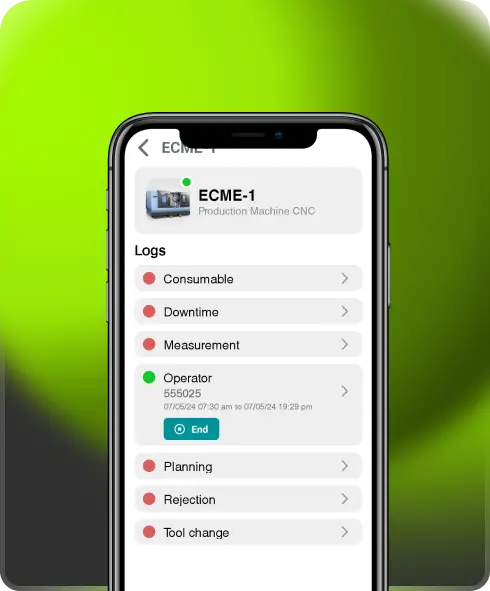
Why Choose Autobits for Predictive Maintenance?
-
Customized
Solutions
-
The priority on
Sustainability
-
Cutting-edge
Technology
-
Ongoing
Support
Implementing Predictive Maintenance with Autobits
Integrating our advanced monitoring systems into your current infrastructure is the first step in putting predictive maintenance into practice. Our team of experts places sensors, IIoT devices, and data-collecting tools on vital equipment in the right places.
After the system is installed, our software begins monitoring the machinery all the time. Key indicators of the health of your machinery, such as temperature, pressure, vibration, and other vital signals, are tracked by sensors. Real-time data collection ensures that you always have access to up-to-date knowledge on the state of your assets.
Our advanced analytics platform analyzes this data using powerful algorithms and machine-learning techniques to uncover patterns and detect anomalies. When the software detects a potential problem, it sends real-time notifications, allowing your maintenance staff to take immediate steps before a minor issue turns into a big failure.
Instead of depending on fixed maintenance intervals, Autobits' predictive maintenance enables you to focus on the equipment that requires the most care. This not only avoids unnecessary downtime but also extends the life of your equipment by addressing issues early on.
Are You Ready to Boost Your Operational Efficiency?
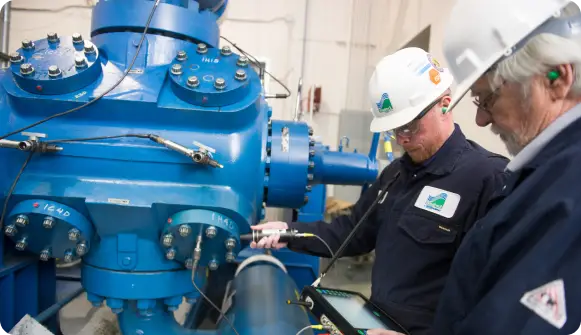
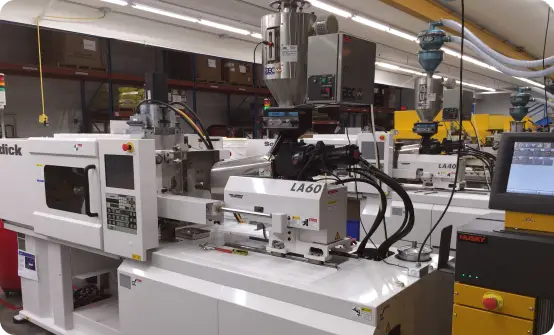