Currently, staying competitive in manufacturing is not just about making goods but making goods efficiently with minimal waste and maximum flexibility. Production monitoring has called to mind clipboards, manual counts, and end-of-shift reports for too long. Imagine if you could know the exact status of your production line from anywhere at any time. This is the power of real-time production monitoring software.
We are now moving beyond the initial ideas of counting parts into a more complete, dynamic view of managing your shop floor.
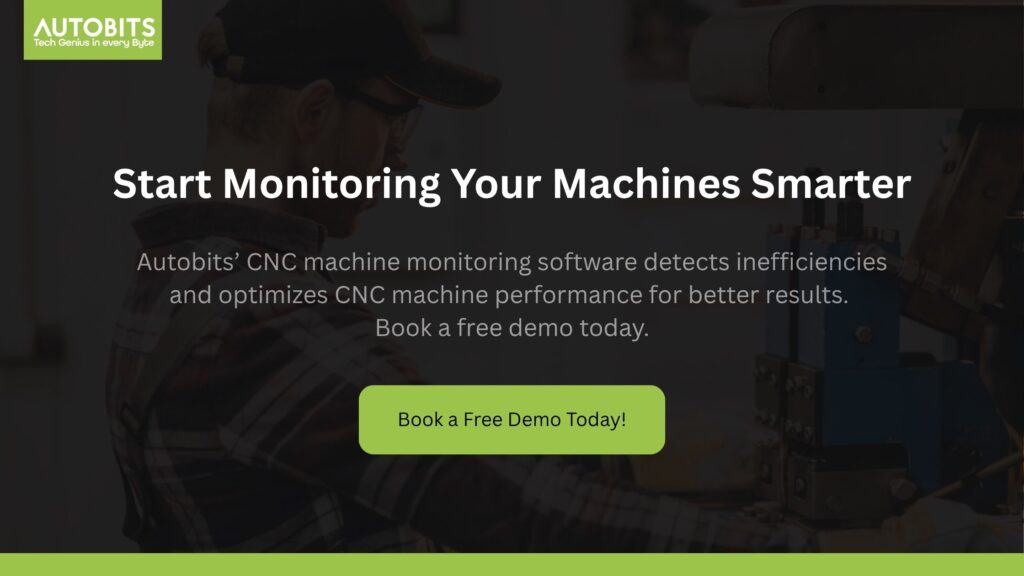
What Does Production Monitoring Encompass?
Production monitoring software captures, analyzes, and displays essential data from your manufacturing processes in real time. While counting finished parts is the basic output, accurate real-time monitoring goes much deeper, providing data about many vital metrics that impact your bottom line.
Let’s consider some of these areas:
Cycle Times:
How long does each product or part progress through an individual production step? Tracking cycle times in real time allows you to find bottlenecks, bad processes, and areas for improvement. Are machines working as fast as they can? Are operators taking too long to do specific tasks?
Scrap and Rework:
Each piece of scrap is wasted material, labor, and machine time. When implementing real-time monitoring, operators can precisely see when and where scrap is being generated and act quickly to reduce losses. The same can be said for rework rates; knowing your rework rates helps you target your quality issues at their source.
Throughput:
This is the speed of productivity. While useful regarding cycle time, throughput is a more specific measure of total line performance. Are you on track to meet your production goals for a particular hour or shift? Real-time information is helpful when checking for deviations right away.
Machine Downtime and Uptime:
Why was a machine shut down? Should it be attributed to an unplanned, planned maintenance or operator breakdown? Having real-time visibility into machine operating status and reason for downtime is paramount for optimizing efficient equipment utilization and scheduling preventative maintenance.
Overall Equipment Effectiveness (OEE):
OEE is the gold standard for manufacturing metrics. It combines availability, performance, and quality into one overall score. OEE can often be auto-calculated with real-time production monitoring software, allowing you to know the actual efficiency of your manufacturing process in real time.
Operator Performance:
While this is not about micromanagement, understanding operator performance in terms of efficiency and adherence to processes can yield important training information and identify areas of needed support.
The Game-Changing Benefits of Real-time Insights
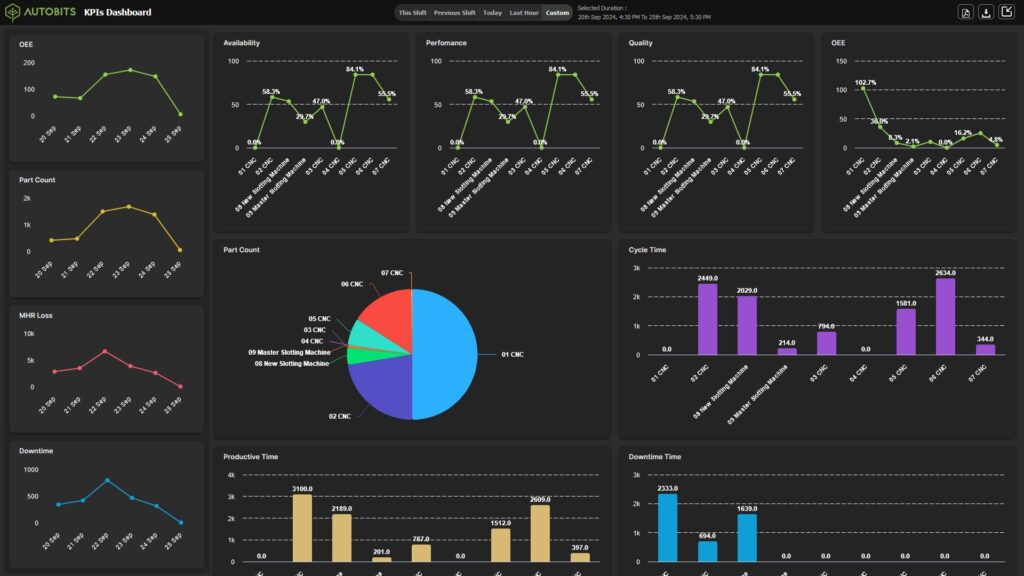
Moving from delayed, aggregated data to real-time production data transforms how you manage your operations. The benefits are profound:
Faster Identification of Issues:
Picture a situation where something like a machine malfunction, a quality defect, or a bottleneck has developed. If you have real-time awareness of that information, you see it immediately instead of 2 hours or even a whole shift later. Real-time information allows you to limit the impact of the issue.
Proactive Problem Solving:
You can anticipate problems instead of waiting for them to escalate before you react. For example, if cycle times were slowly rising on a machine that was not experiencing an apparent breakdown, it might be a tool wear issue, which you can address before a failure occurs.
Optimized Resource Allocation:
Understanding in detail which machines are operational and which are idle and the reasons behind them gives you the opportunity to reallocate resources (staff, materials, or other machines) to increase output and decrease time spent waiting.
Reduced Waste and Rework:
By identifying the exact moment and cause of scrap or defects, you can immediately take corrective action, drastically reducing material waste and rework costs.
Enhanced Quality Control:
Real-time data allows you to monitor process parameters and identify deviations that could lead to quality issues before they result in a non-conforming product.
Improved Decision-Making:
With precise, real-time data, managers can make informed, data-driven decisions. Is a particular order a priority? Do we need to adjust staffing? Is a machine getting close to its maintenance schedule? You can find your answers quickly.
Increased Accountability and Transparency:
When everyone on the shop floor monitoring system has access to the same real-time metrics, it fosters a culture of transparency and shared responsibility for performance.
How it Leads to Faster Decision-Making
There is an undeniable correlation between real-time insights and faster decision-making. With real-time data, decisions will not rely on instinct, trends, historical averages, or stale data. These problems, left unaddressed, could create the following issues:
- Delayed corrective actions: Problems develop, leading to further losses
- Underutilization of available resources: Machines being idle or operator(s) being underutilized
- Missed opportunities: Production capacity not being used at potential
In the presence of real-time production data, the duration of the decision-making loop is significantly shortened. An anomaly is identified and examined, and changes are made in minutes rather than hours or days. This level of agility truly distinguishes Category 1 manufacturers from everyone else. It enables you to take action rapidly, take advantage of rising opportunities, and respond to risks before they develop.
Beyond the Hype: Implementing Real-time Monitoring
Implementing a robust production monitoring software solution involves more than just installing sensors. It involves careful planning, integrating with current systems to ensure an efficient transfer of data (ERP or MES system), and developing a proactive approach to improving the data. However, regarding increased productivity, reduced costs, and enhanced competitiveness, the return on investment cannot be overstated, and production monitoring software is necessary for today’s manufacturers.
Don’t just count parts. Know your whole production story in real time to unleash the complete picture of your manufacturing opportunity.
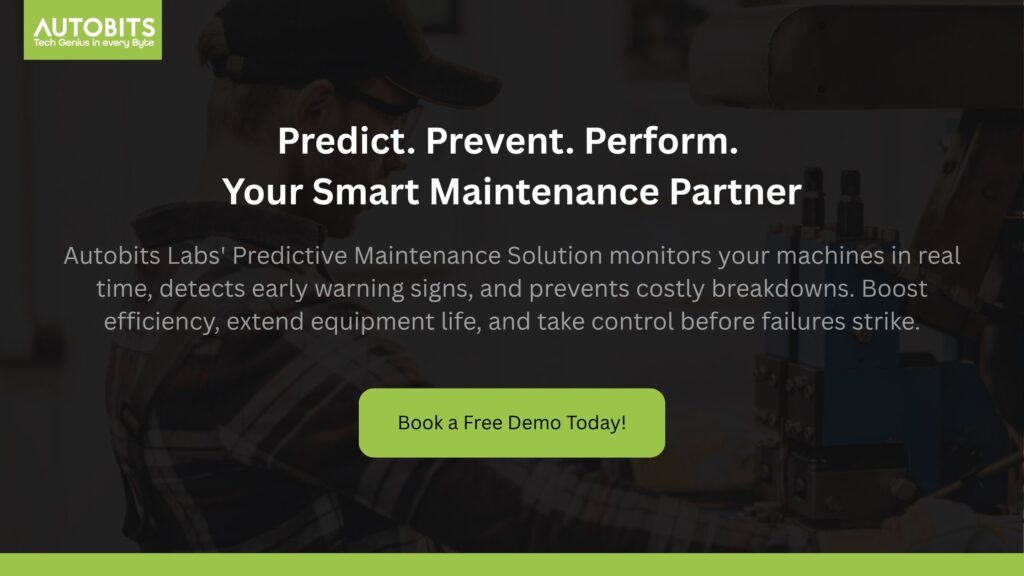
Frequently Asked Questions (FAQs) about Real-time Production Monitoring Software
What is real-time monitoring software for production?
Real-time monitoring software for production measures, analyzes, and shows the data from your manufacturing operations while they happen. It allows you to see cycle times, machine status, scrap rates, and throughput, providing immediate visibility and allowing for rapid decisions.
How is real-time monitoring better than traditional methods in manufacturing?
Traditional methods often involve reporting based on manual data collection throughout the shift and compiling it into an end-of-shift report, ultimately leading to late or inaccurate information. Real-time monitoring software automates measuring and capturing the data directly from the machines and systems, giving constant visibility (in real-time) and reports that support immediate, proactive decision-making.
What key metrics can I track with production monitoring software?
Beyond just counting parts, you can track critical metrics such as:
1. Cycle Times
2. Scrap and Rework Rates
3. Throughput
4. Machine Downtime and Uptime Reasons
5. Overall Equipment Effectiveness (OEE)
6. Energy Consumption (in some advanced systems)
7. Operator Performance
What are the main advantages of using real-time production monitoring?
The key advantages include identifying problems sooner, identifying issues before they happen, using resources more efficiently, minimizing waste and reworks, quality control, making better decisions, and providing accountability and transparency throughout the shop floor.
Is real-time production monitoring software just for big manufacturers?
Not really! Big enterprises can realize the benefits of production monitoring, but the scalability of production monitoring software can also be very valuable for small and medium manufacturers (SMEs). The benefits of efficiency and reducing waste are the same, no matter the manufacturer’s size.
Is it challenging to integrate real-time production monitoring software into current systems?
Integration difficulty depends on the current infrastructure (ERP, MES, SCADA, etc.) and your real-time production monitoring solution. Standard production monitoring systems offer flexible APIs and connectors to ease integration. It is important to choose vendors with experience integrating in manufacturing environments similar to your own.