In manufacturing, the focus is on productivity improvement and waste reduction. The most powerful tool to improve productivity and minimize waste in manufacturing is OEE – Overall Equipment Effectiveness.
OEE provides a measure of how effectively your manufacturing operation is functioning and identifies areas for improvement. In this blog, we will clarify what OEE is, how it is determined, and how it can help identify opportunities for US manufacturers to improve productivity and reduce waste.
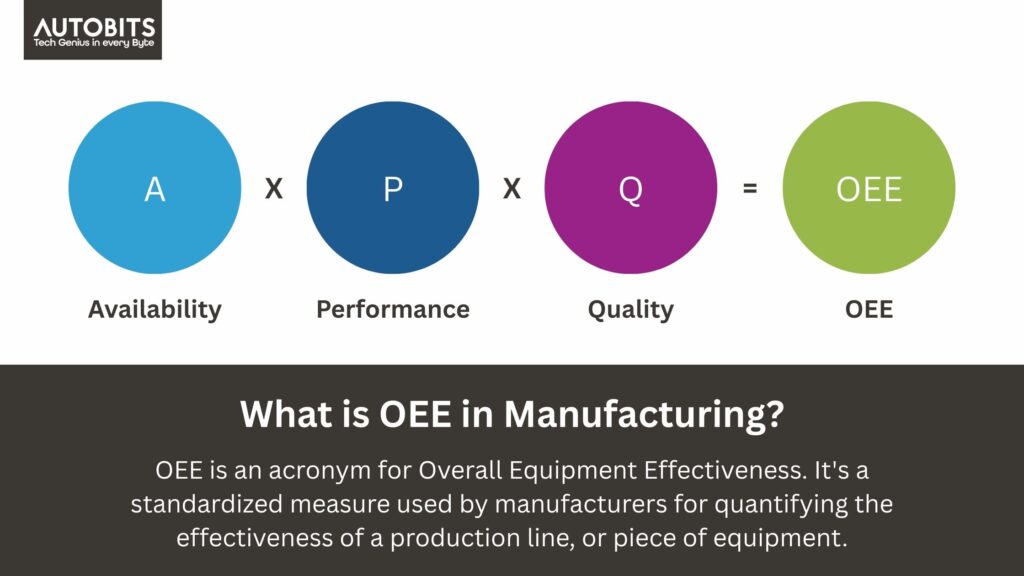
What Does OEE Stand For?
OEE is an acronym for Overall Equipment Effectiveness. It’s a standardized measure used by manufacturers for quantifying the effectiveness of a production line, or piece of equipment. The goal of OEE is to identify and eliminate losses, so that companies can maximize the potential of thier machines and systems.
OEE takes into account three core factors:
- Availability – How often is the machine running when it’s supposed to?
- Performance – Is the machine running at its maximum possible speed?
- Quality – How many of the produced units are defect-free?
Why is OEE Important in Manufacturing?
Overall Equipment Effectiveness (OEE) is considered the gold standard for measuring manufacturing productivity and provides an unambiguous, quantitative view of how a manufacturing operation is functioning. OEE’s importance results from several important factors that impact a manufacturer’s efficiency, competitiveness, and profitability.
Maximizes Productive Time
OEE measures the percentage of manufacturing time that is truly productive, determined by three components: Availability, Performance, and Quality. OEE of 100% means that only good parts are produced as fast as possible and there is no downtime. OEE tracking allows manufacturers to track where productivity losses are happening – whether due to how much downtime there is on equipment, too slow cycles, or defective parts – and take specific action on those issues.
Drives Continuous Improvement
OEE is the basis of any continuous improvement initiative. The standardized measurement OEE provides is critical for teams to establish the baseline level of performance, determine realistic targets based on capacity, and monitor progress moving forward. When teams are consistently using OEE metrics to understand production performance variations, it generates hard data that can highlight bottlenecks or inefficiencies. Manufacturers are also using OEE to test corrective actions and monitor the impacts of those actions on production performance.
Reduces Costs and Increases Capacity
Improving OEE is generally more cost effective than spending money on new equipment, adding new shifts, or outsourcing production. By getting more out of your existing assets, you may be able to increase output and capacity without large capital expenses. This leads to a better utilization of your assets, less requirement for capital expenditure, and a better return on the investment.
Improves Quality and Reduces Waste
OEE focuses on not just how much you produce, but how good it is. By measuring the percentage of good parts to total parts made, manufacturers can swiftly identify and rectify quality issues, minimizing waste, rework and potentially costly recalls.
Improves Maintenance and Reduces Downtime
OEE data helps manufacturers identify the relationships between downtime and inefficiencies. This added information helps manufacturers plan proactively for maintenance, like preventive or predictive maintenance, which can reduce unplanned downtime, extend equipment life, and reduce repair costs.
Supports Data-Driven Decision Making
OEE gives manufacturers real-time visibility into their operations, enabling them to make informed decisions based on relevant data. This transparency assists manufacturers in allocating resources, planning production, and planning improvement projects.
Boosts Competitiveness and Profitability
OEE enables manufacturers to maximize productivity, minimize costs, and enhance quality, ensuring they remain efficient and reliable while also being competitive. Industry competitiveness is often based on some factor of efficiency, as higher OEE directly translates into higher profitability and a better competitive position.
In short, OEE is important in manufacturing because it provides an all-in-one, actionable metric that highlights efficiency, quality, and profit, making it a foundational element of new modern manufacturing best practices.
How OEE Is Calculated
The OEE (Overall Equipment Effectiveness) is expressed in the multiplication of three main elements: Availability, Performance, and Quality. Each element addresses a different type of loss in the manufacturing process, which gives OEE an all-encompassing dimension of manufacturing efficiency.
OEE Formula
OEE = Availability × Performance × Quality
Breakdown of the Three OEE Factors
Calculating Availability:
Measures the percentage of scheduled production time that the equipment is running.
Formula: Quality = Good Unit Output / Actual Output
Where: Run Time = Planned Production Time − Stop Time (includes both planned and unplanned stops).
Calculating Performance:
Measures how fast the equipment runs as a percentage of its designed speed.
Formula: Performance = Actual Output / Theoretical Output
Ideal Cycle Time is the fastest possible time to produce one unit.
Calculating Quality:
Measures the percentage of good units produced out of the total units started.
Formula: Quality = Good Unit Output / Actual Output
Simplified OEE Calculation
Alternatively, OEE can be calculated directly as:
OEE = Good Count x Ideal Cycle Time / Planned Production Time
This formula gives the same result and is sometimes used for quick calculations.
How is OEE Calculated?
OEE Calculation Example:
Suppose:
- Planned Production Time = 420 minutes (25,200 seconds)
- Stop Time = 50 minutes (3,000 seconds)
- Run Time = 370 minutes (22,200 seconds)
- Total Count = 19,271 units
- Good Count = 18,848 units
- Ideal Cycle Time = 1 second/unit
Calculate each factor:
- Availability = 22,200 / 25,200 = 0.881
- Performance = (1 × 19,271) / 22,200 = 0.868
- Quality = 18,848 / 19,271 = 0.978
OEE = 0.881 × 0.868 × 0.978 = 0.747 (or 74.7%)
OEE is determined by calculating Availability, Performance, and Quality and multiplying the results. Each of the three refers to a different type of production loss. Using OEE will give you a simple and actionable measure to better understand your manufacturing productivity, and ways you can improve it.
What is a Good OEE Score?
Here’s how OEE percentages are typically interpreted:
- 100% – Perfect production: no downtime, full speed, no defects.
- 85% – World-class level in discrete manufacturing.
- 60%-85% – Room for improvement.
- Below 60% – Significant losses; improvement needed.
Need Help Improving Your OEE? Our industrial automation experts at Autobits Labs are on a mission to help manufacturers all around the world unlock more productivity through smart OEE strategies. Schedule a free consultation call with our OEE expert and receive individualized insights on how to improve your production efficiency. Schedule a Call Now |
How to Improve OEE in Manufacturing
Enhancing performance and Overall Equipment Effectiveness (OEE) can have a larger impact on your overall production efficiency. To consistently improve OEE, you need to take a systematic approach focused on the fundamental factors of availability, performance, and quality. Here are researched methods and best practices:
Automate Data Collection and Reporting
Use an automated system to record real-time data from your equipment on performance, downtime, and production output. You will reduce the potential for human error, ensure consistent data from your available data sources, and use the data to provide real-time decision analysis.
Identify and Address the Six Big Losses
The next step is to categorise OEE losses into six buckets: changeovers, breakdowns, minor stoppages, reduced speed, start defects, and scrap. Start with the biggest losses first and focus improvement efforts on the larger losses first, you may wish to use tools like a Pareto analysis, and waterfall charts to help focus improvement efforts on more devastating or losses.
Implement Preventive and Predictive Maintenance
Identify a scheduled preventive maintenance plan for your equipment to avoid unplanned downtime and to help extend the life of the assets. Integrate predictive maintenance using real time and analytical data to anticipate possible equipment failures before they happen.
Visualize OEE Performance
Show real-time OEE metrics on the shop floor for visibility and operator engagement. This clarity allows teams to rapidly understand problems while establishing a mindset and behaviors of accountability and continuous improvement.
Assign a Digital or Project Champion
Assign a person or team to be responsible for OEE initiatives so you have someone for ownership to create consistency, implement initiatives, and push through the opposition to change.
Involve Operators and Foster Continuous Improvement
Involve frontline workers in recording every production stop and soliciting their input. Use continuous improvement approaches (for example, Kaizen or PDCA) to systematically identify root causes and drive sustained improvements.
Invest in Real-Time Production Monitoring Software
Utilize sophisticated monitoring systems to assess equipment status, analyze bottlenecks, and provide data-driven insights to continually optimize these processes.
Leverage Lean, Six Sigma, and TPM Methodologies
Implement best practices from Lean Manufacturing, Six Sigma, and Total Productive Maintenance (TPM), to reduce waste, minimum variability, and maximize equipment effectiveness.
By consistently leveraging these strategies, manufacturers can provide a substantial increase to OEE, which will increase productivity, reduce costs, and improve product quality.
Tools and Technologies to Track OEE
In the United States, many manufacturing plants use modern tools like:
- MES (Manufacturing Execution Systems)
- IoT-based sensors and automation
- Cloud-based OEE software (like Vorne XL, MachineMetrics, etc.)
- Lean Six Sigma tools
These tools provide real-time OEE dashboards, enabling quick decision-making and continuous monitoring.
Trusted OEE Software by Autobits Labs You’re not alone in having too many options to choose from, but Autobits Labs is one of the best OEE software solution providers in the United States. We provide the best OEE tools in the US with up-to-date dashboards, access to machine integration, IoT sensors, and customizable analytics – all to enable your manufacturing process. Looking for a powerful, scalable OEE software solution? Let Autobits Labs build it for you. Learn More About Our OEE Software |
OEE in Lean Manufacturing and TPM
OEE is a pivotal measure in Lean Manufacturing and TPM (total productive maintenance) that supports both methods’ goals of reducing waste and maximizing efficiency. Manufacturers can use OEE as a starting point to conceptualize Kaizen (continuous improvement) initiatives and the progress of TPM techniques.
FAQs About OEE (Overall Equipment Effectiveness)
What is a good OEE score for a manufacturing plant?
A world-class score is 85% or greater, while most companies begin between 40% to 60%, meaning significant opportunities for improvement exist.
Can OEE be used in any kind of manufacturing?
Absolutely! OEE is used in discrete, batch, and continuous manufacturing in sectors such as automotive, food & beverage, packaging, electronics, and others.
Is OEE only about machines?
OEE does hone in on equipment performance, but also includes performance issues connected to operators, processes, and materials.
What is the difference between OEE and Efficiency?
Efficiency measures output vs. input and typically of a single resource. OEE provides a more complete view of performance by including time, speed, and quality, therefore providing a broader view of productivity.
How often should OEE be tracked?
Ideally, it should be reported in real-time, but even daily, weekly, or shift recap reports can be helpful and provide actionable performance insights.
Conclusion
Overall Equipment Effectiveness (OEE) goes well beyond a performance metric; OEE is an effective approach to advancing productivity, reducing losses, and increasing profitability.
By tracking and analyzing OEE, U.S.-based manufacturers gain a vital advantage in an increasingly fast-paced industrial environment.
Whether you are a plant manager, operations leader, or maintenance engineer, being able to apply OEE to your operation can help you achieve real, impactful, and measurable improvement… in your production process.